Logistics are tough and can cost 12 to 20% of eCommerce revenues. Given the cyclical nature of many industries, it can be difficult to balance the cost of investing in operations to support high-volume sales seasons against the possibility of missed sales opportunities if resources are too slim. But that doesnโt mean itโs impossible.
Thankfully, you can use a whole set of tools and techniques to handle your seasonal demand issues.
Letโs take a closer look at what seasonal demand is, the challenges it presents, and how you should think about it. Then, you can learn how to navigate seasonal demands on inventory without increasing off-season storage costs or over-extending internal resources during peak season.
What Is Seasonal Demand?
Seasonal demand refers to fluctuations in purchasing behavior at different times throughout the year. These variations may be related to holidays, weather changes, cultural events, or industry-specific trends. Thankfully, brands can often predict seasonal demand, making it easier to plan accordingly.
For instance, retail sales often surge during the holiday season in December, while the demand for sporting goods and outdoor equipment spikes in the spring and summer. Similarly, fashion industries experience seasonal demand as consumers update their wardrobes for different weather conditions.
In the agricultural sector, seasonal demand is highest in the harvest periods when fresh produce is at its best. In the travel industry, peak seasons align with school vacations and public holidays. Understanding these patterns is important for businesses to optimize their inventory levels to meet customer demands without overstocking during off-peak times.
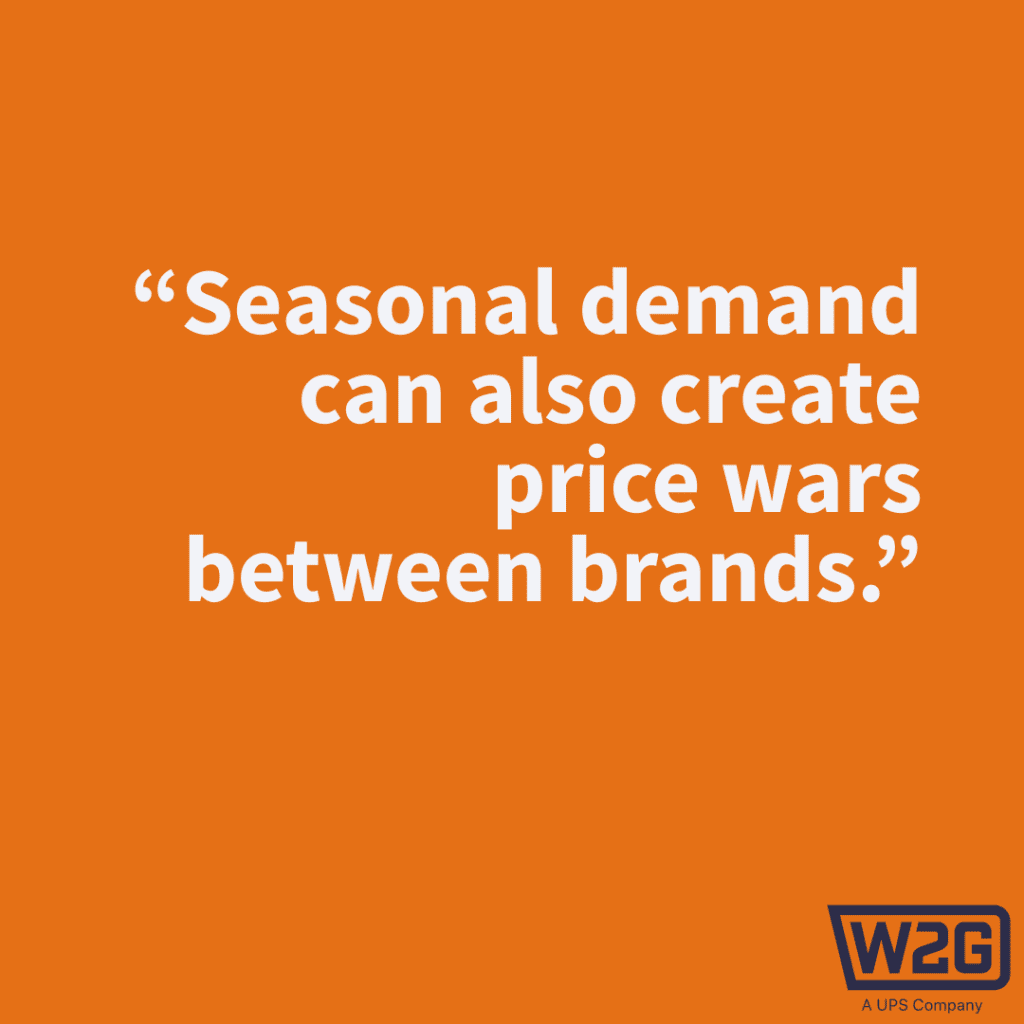
Why Seasonal Demand Creates Issues for Distribution
Seasonal demand can pose significant challenges for distribution due to the wide fluctuations in the need for stock.
During peak seasons, businesses must scale their operations to handle increased order volumes, which can strain logistics networks and lead to delays or stockouts. Conversely, maintaining excess inventory during off-peak periods can lead to high storage costs and capital tied up in unsold goods.
Seasonal demand can also create price wars between brands. As competition increases during peak seasons, many brands offer discounts and reduce profit.
For example, a retailer might struggle to stock enough winter clothing in anticipation of a cold season, only to face unsold inventory if the weather is milder than expected. Similarly, the surge in demand for electronic gadgets during back-to-school periods can overwhelm supply chains, leading to limited customer supply.
Effective demand forecasting and flexible supply chain strategies are essential to mitigate these issues. They ensure that businesses can manage seasonal inventory efficiently, respond swiftly to changes in consumer behavior, and maintain cost efficiency.
How Should Brands & Retailers Think about Seasonal Demand?
Brands and retailers are starting to think of seasonal demand โ and the inventory to satisfy it โ as year-round sales cycles that need acute attention to detail. However, decision-makers are often only left with 2 unsatisfying options.
One is to lock into a storage and fulfillment contract covering peak capacity and pay for unused storage during their off-season. The second is to keep operations tight year-round, resulting in over-extending internal resources during busy seasons. However, leveraging on-demand warehousing gives brands and retailers a much more attractive third option for managing seasonal inventory.
How On-Demand Warehousing Supports Seasonal Inventory
With on-demand warehousing, online retailers only pay for the warehouse space and labor they need when they need it. This allows retailers to scale up operations quickly to meet seasonal demand without committing to the same order volume in the off-season. This new option makes seasonal sales much more profitable by lowering operating costs year-round.
On-demand warehousing is made possible by aggregating the volume of multiple online retailers to negotiate better storage rates and Service Level Agreements (SLAs) for seasonal or cyclical demand.
Also known as co-warehousing, this sharing of resources benefits brands and 3PLs looking for guaranteed seasonal inventory order volume. According to McKinsey, when compared to dedicated fulfillment, co-warehousing can save an average of 7โ9% of supply chain costs.
The Problem of Peak Season (And Seasonal Demand) Isnโt Going Away
In fact, 73% of eCommerce survey participants expect this yearโs holiday sales to be higher than in previous years. This increase is by design: 84% of survey participants implement longer, more aggressive promotional calendars. Meanwhile, 50% introduce new deal days, coupons, or promotions to encourage more sales.
Seasonal Demand and Profitability
Seasonal demand can often make or break a merchantโs top-line revenue for the year, but it also creates a unique set of supply chain challenges that threaten the bottom line.
Understanding the effect of year-round fulfillment and storage costs on the margin of seasonal sales helps brands tap into seasonal demand and grow their business.
The first impact of seasonal demand is a fluctuation in the amount of inventory storage space needed. The graph below shows an example of a merchant whose sales peak during November and December each, driving up their storage needs by more than 100% compared to their off-season in the early summer.
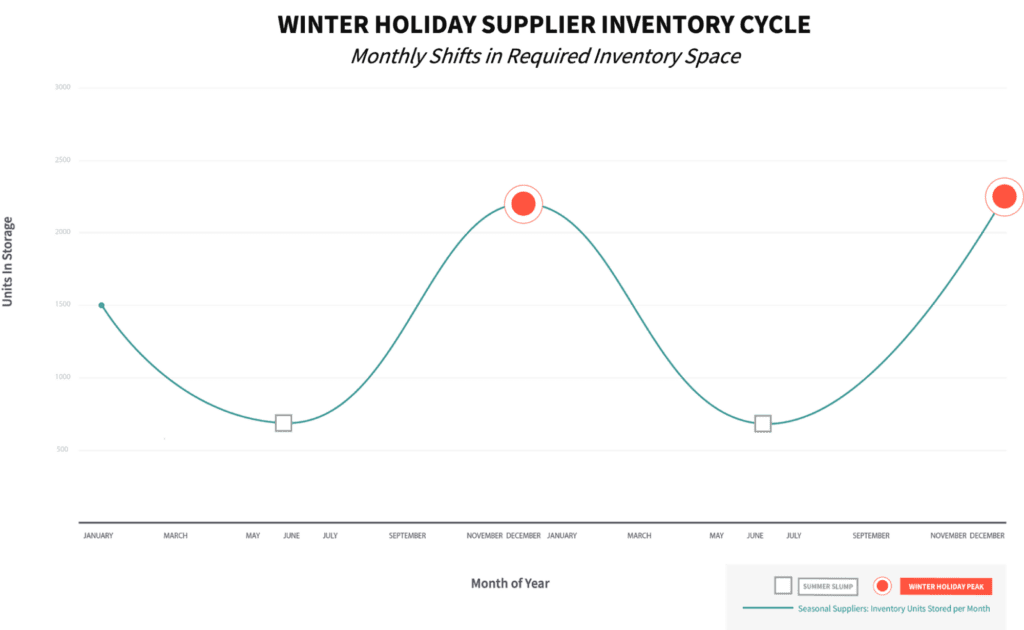
In this example, contracting with a traditional 3PL based on peak seasonal inventory means paying for more than twice the storage space needed for most of the year. Conversely, contracting based on off-season needs and opting for a short-term seasonal contract can mean steep premiums during the peak season. Meanwhile, available warehouse space continues to decline each year โ including ad hoc space for their seasonal inventory.
What Are Some Strategies for Managing Seasonal Inventory?
Seasonal demand creates challenges around warehouse space, labor, and evolving customer expectations for eCommerce shipping. The 4 major challenges merchants face in managing seasonal inventory are:
1. Required Year-Round Contracts & Inflexible Agreements Can Devastate Seasonal Retailers
Seasonal retailers may only make a small percentage of annual sales during some months. However, those same retailers still pay for warehouse space based on peak demand.
2. Storage Space Is Limited During Peak Seasons
Warehouse space is at a premium, and peak seasons โ like holiday shopping โ only compound this problem. In fact, Amazon has continued tightening FBA inventory limits and doesnโt appear to be returning anytime soon.
3. Warehouse and Fulfillment Rates Spike with Demand
As demand for warehouse space and fulfillment services increase, prices often do too. Merchants may move more inventory in their busy season but at greater operational cost.
4. Supply Chain Speed Suffers
Suppliers may be forced to reduce inventory or curb production if warehouses cannot cope with large-scale shifts in seasonal storage and fulfillment needs. In turn, this can impact order fulfillment speeds โ resulting in more frequent stockouts, slower delivery times, and decreased customer satisfaction.
So, despite these challenges, how can merchants manage seasonal inventory? The first step is through proactive supply chain planning, which looks like this:
- Accurate Demand Forecasting โ Use past sales data, current industry trends, and geographic demand patterns to predict seasonal demand. This helps merchants manage profit margins and operating costs more effectively, improving their business.
- Distributed Inventory โ Often, seasonal demand is also regional. For example, ski jackets will likely never sell as well in warmer regions as in colder ones. However, when merchants stock inventory in areas of greatest demand, they can fulfill orders with ground shipping in 1 to 2 days without relying on next-day delivery.
- Offloading Slow-Moving SKUS โ Slow-moving inventory can eat up profits with long-term storage costs. Seasonal retailers should consider offering deep discounts on slow-moving SKUs. By bundling older inventory with newer products in buy-one-get-one promotions, eventually, you can liquidate obsolete inventory.
- Streamlined Fulfillment โ Streamline fulfillment through a plug-and-play supply chain solution that enables aggregated and comparative views, sales performance, and order profiles by channel and geographic market. Ultimately, this allows brands to make strategic decisions around inventory allocation and marketing spend.
Seasonal Demand KPIs and Metrics
How are you supposed to know if youโre keeping up with seasonal demand well?
The answer is in key performance indicators (KPIs) and metrics. These help businesses monitor their inventory levels, sales performance, and overall supply chain efficiency, providing valuable insights to make data-driven decisions.
Here are some essential KPIs and metrics to consider when tracking your seasonal inventory management:
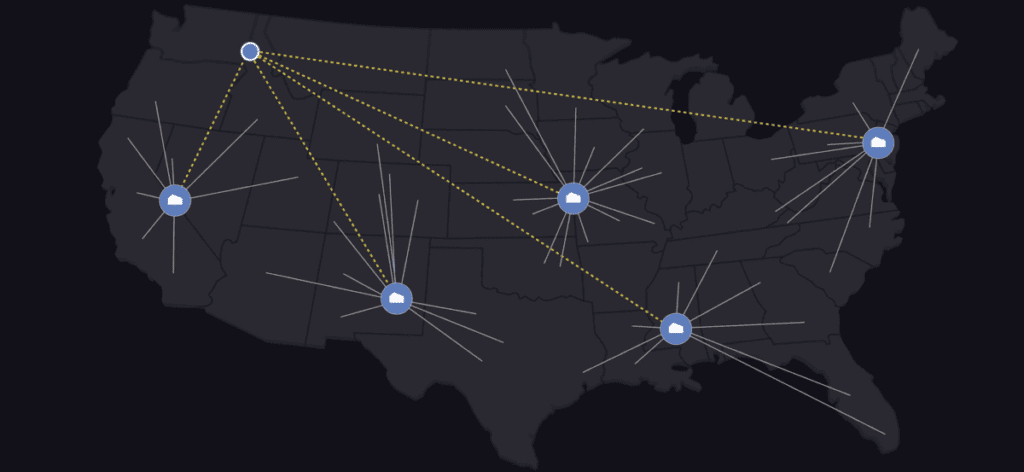
Total Inventory Turnover
Total inventory turnover measures how often inventory is sold and replaced over a specific period. Itโs calculated by dividing the cost of goods sold (COGS) by the average inventory during that period. This metric is crucial for seasonal inventory, as it indicates how efficiently a company manages its stock.
A high inventory turnover ratio suggests a business sells products quickly, which is ideal during peak seasons. Conversely, a low turnover ratio may indicate overstocking or slow-moving inventory, leading to increased storage costs and potential obsolescence. Monitoring this KPI helps businesses optimize their inventory levels, ensuring they have enough stock to meet demand without overcommitting resources.
Number and Rate of Stockouts
Stockouts occur when an item is out of stock and unavailable for purchase. The number and rate of stockouts are critical metrics for seasonal inventory management. They highlight how often a business fails to meet customer demand, leading to lost sales and potential damage to customer satisfaction and brand reputation.
Calculating the stockout rate involves dividing the number of stockouts by the total number of items sold. High stockout rates during peak seasons indicate poor inventory planning and forecasting. Reducing stockouts requires accurate demand forecasting, effective inventory replenishment strategies, and maintaining safety stock levels to cushion against unexpected demand surges.
Days to Sell Inventory
Days to sell inventory (DSI), also known as inventory days on hand, measures the average number of days it takes for a business to sell its entire inventory. Itโs calculated by dividing the average inventory by the COGS and multiplying by 365 days. This metric is particularly relevant for seasonal inventory, reflecting how long products remain in stock before being sold.
A lower DSI indicates that inventory moves quickly, which is desirable during peak seasons. On the other hand, a higher DSI suggests slow-moving inventory, which can lead to increased holding costs and potential markdowns. Monitoring DSI helps businesses adjust their purchasing and sales strategies to align with seasonal demand patterns.
Average Inventory Levels
Average inventory levels represent the average amount of inventory held over a specific period. This metric is calculated by taking the sum of the beginning and ending inventory for a period and dividing the result by 2. For seasonal inventory management, maintaining optimal average inventory levels is crucial to effectively balancing supply and demand.
High average inventory levels during off-peak seasons can tie up capital and increase storage costs. Conversely, low inventory levels during peak seasons can lead to stockouts and lost sales. By tracking this metric, businesses can better plan their inventory purchases and storage needs, ensuring they have the right amount of stock at the right time.
5 Seasonal Inventory Management Methods
There are 5 main methods for managing inventory, and any of them could be appropriate for managing seasonal inventory, depending on SKU profile, sales velocity, current business operations.
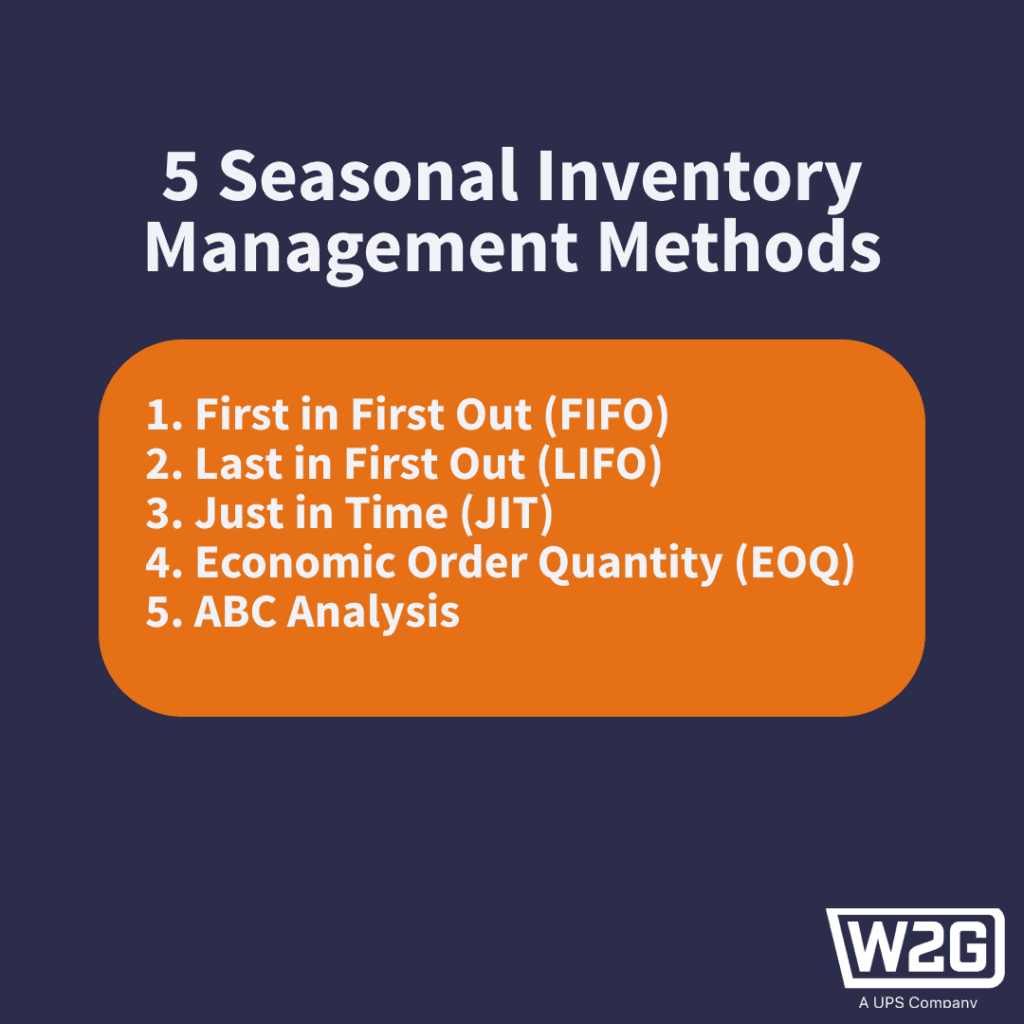
1. First in First Out (FIFO)ย
The FIFO inventory method uses the oldest inventory (first in) to fulfill orders first (first out). The FIFO method is appropriate for perishable and highly seasonal products and can increase margins on items that experience price hikes during times of high seasonal demand.
2. Last in First Out (LIFO)ย
The LIFO inventory method uses the newest inventory (last in) to fulfill orders first (first out). The LIFO method can quickly recoup expenses on products acquired at a premium seasonal price, either at the raw materials level or as finished goods.
3. Just in Time (JIT)
The JIT inventory method is most commonly used by SMBโs because it requires the least intensive demand forecasting. JIT supply chains are replenished on an as-needed basis. Theyโre a high-risk supply chain management strategy that can reward merchants with increased capital. But as weโve seen with recent supply chain disruptions, they can leave merchants with empty shelves when seasonal demand hits.
4. Economic Order Quantity (EOQ)
The EOQ method determines ideal inventory levels using 3 metrics: customer demand, acquisition cost, and holding cost. The EOQ method can drastically cut down on inventory carry costs but requires advanced demand forecasting models supported by a lengthy sales history.
5. ABC Analysis
An ABC analysis prioritizes SKUs by lumping them into 3 categories:
- High-value products with a low contribution margin
- Mid-Value products selling at a mid-range velocity
- High-velocity products with low margins
An ABC analysis helps merchants prioritize the SKUs that are ultimately driving the profitability of their business and may prompt them to reconsider their product profile entirely.
4 Ways On-Demand Warehousing Helps Meet Seasonal Demand
Without the proper warehousing and fulfillment solution, seasonal suppliers may spend a significant portion of their annual revenue paying for storage space they donโt need. Hereโs how on-demand warehousing can help:
1. Complete Storage Scalability
On-demand warehousing provides businesses with complete flexibility over the levels of inventory they maintain year-round. Warehouse space can be scaled up or down as needed, and with flexible contracts and no start-up fees, theyโre a low-risk option that minimizes investment in fixed assets.
Businesses pay only for the space they use when they use it, and rates are consistent year-round. This enables season merchants to keep overhead low during the off-season and rapidly scale up their inventory in time for the busy season without being sidelined by excessive costs or insufficient storage space.
2. Real-Time Inventory Status & Restock Alerts
By combining their network of warehouses with software, the leading on-demand solutions provide businesses with real-time insights. This includes inventory status across each warehouse location, the status of outstanding deliveries, and in-process shipments. The most advanced systems also set automated re-order points and deliver alerts when inventory drops below a certain threshold.
3. Demand Planning & Sales Forecasting
As supplier data regarding inventory turnover, seasonal demand, and customer deliveries accumulate within the system over time, businesses can leverage the on-demand solution to develop sales and demand forecasts. This allows them to plot out required inventory levels over the year effectively. Ultimately, companies can use these insights to optimize the amount of inventory they maintain year-round, thereby avoiding the costs of excess storage space and protecting against potential stock outages.
4. 2-Day Ground Delivery
Looking beyond seasonal inventory management, on-demand warehouses offer a distributed network of warehouses to enable nationwide 2-day ground delivery. With 57% of shoppers waiting until December to purchase, a nationwide 2-day ground delivery network is a competitive advantage for attracting last-minute convenience shoppers.
However, with the arrival of on-demand warehousing and fulfillment in the logistics space, businesses now have a much more flexible solution for managing seasonal demand.
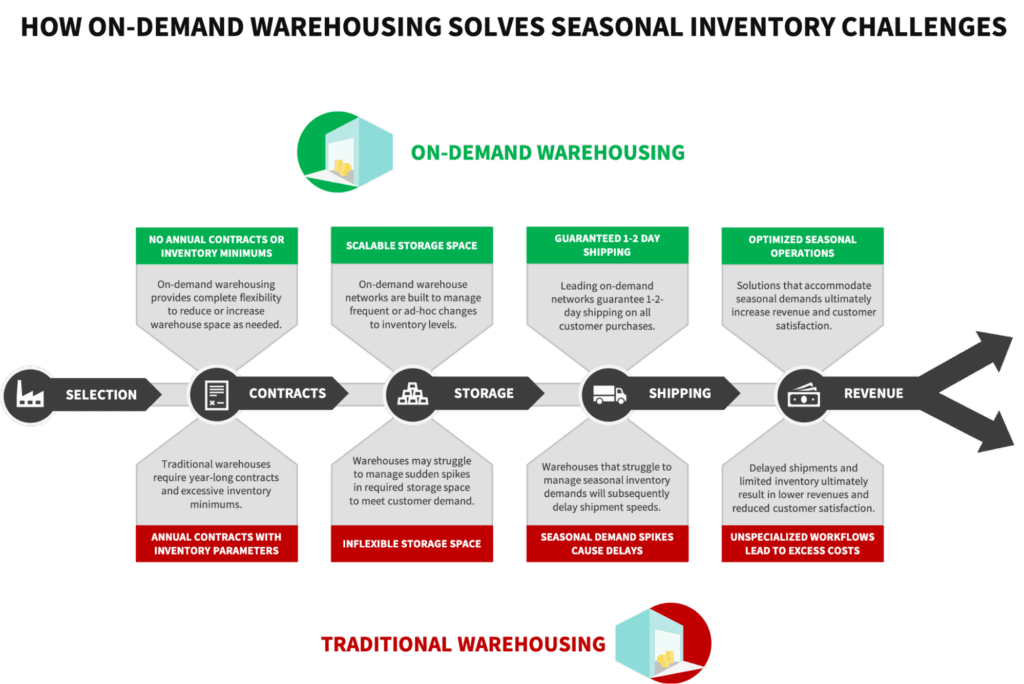
Flexibility Is the Key to Seasonal Inventory Management
As the winter holiday season approaches, many seasonal suppliers are preparing their supply chains for an uptick in demand. Without the appropriate warehousing and inventory management strategy, several will sacrifice margins to elevated storage costs.
With on-demand warehousing, seasonal inventory management can now be transformed from a pain point to a growth lever.
โTo learn how Ware2Go can help your business manage seasonality, reach out to one of our logistics experts.