Did you know that stockouts cost businesses in the US and Canada a staggering $350 billion annually? In fact, reports show that stock availability is one of the top three factors influencing a customer’s choice of retailer.
To avoid the nightmare of stockouts, you need to have the right amount of stock on hand. But how do you strike the perfect balance between preventing stockouts and minimizing inventory carrying costs?
That’s where the safety stock calculation comes in.
Let’s explore the world of safety stock formulas, learn how to calculate them, and understand how much stock you need to manage your inventory successfully to keep customers happy.
What Is Safety Stock?
Safety stock is when a company orders additional inventory to reduce the risk of an item becoming out of stock.
Safety stock allows your supply chain to proceed as normal in the event of high-frequency customer demands, delays with suppliers, failure not to place orders in time, and inaccurate market forecasts.
What Is the Purpose of Safety Stock Calculation?
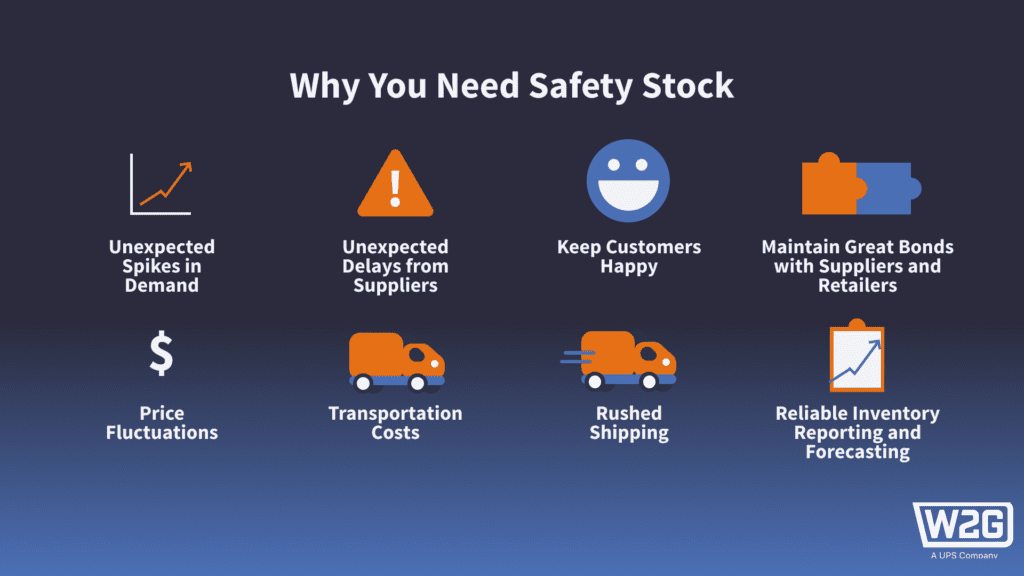
According to IHL Group, a global retail and advisory firm for retail and hospitality, retail loss due to stockouts increased by an alarming 17.7% in the US alone in 2023.
The real risk of a stockout, especially for fast-growing brands, is disappointing and losing customers.
Thankfully, safety stock can help brands avoid not having enough inventory to match customersโ demand, and here are some benefits of safety stock:
- Be ready for unexpected spikes in demand โ This was perfectly illustrated by the panic-buying early in the COVID-19 pandemic and the lifestyle changes that came about later in the pandemic as consumers transitioned to life at home. Safety stock helps you manage fluctuations in demand caused by seasonal changes, changes in customer demand, or a competitor entering or exiting the market.
- Prepare for unexpected delays from suppliers โ Supplier delays can be caused by many factors, from inclement weather to raw material shortages to operational shutdowns. With safety stock, you have enough inventory to cover customersโ demands, even if suppliers are operating as usual.
- Keep customers happy โ The 2023 KPMG Consumer Pulse holiday report shows that stock availability is among the top three factors buyers consider when selecting which eCommerce retailer to buy from. This means you must ensure customers receive their orders without disappointment, regardless of your business/industry circumstances.
- Maintain great bonds with suppliers and retailers โ Keeping safety stock on hand reduces the need for urgent reorders, which can disrupt your suppliers’ operations. By providing a steady workload and preventing stockouts, you build good relationships with suppliers and retailers by avoiding rushing orders or having to expedite shipping thus avoiding putting strain or pressure on them.
- Avoid price fluctuations โ If your products are evergreen and you can afford to hold excess inventory, it may make sense to purchase safety stock when prices are low. That way, if prices jump up unexpectedly, you can hold off on your replenishment order to see if prices level out.
- Save on extra transportation costs โ During the holiday season, some merchants may feel forced to pay for expedited transportation methods to get inventory on the shelves in time for holiday sales. With enough safety stock, you can weather transportation slow-downs without risking stockouts or expediting a replenishment order.
- Avoid cost due to rushed shipping โ Not having enough inventory can cost you more than lost revenue, such as increased administrative and warehouse payroll costs or suppliers charging a premium for rushed delivery.
How Much Safety Stock Do You Need?
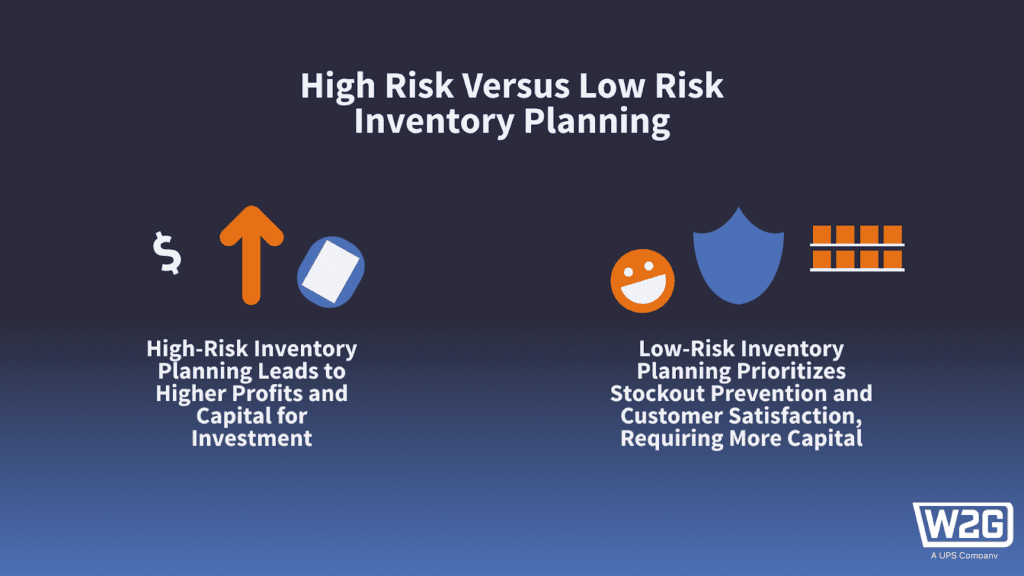
The simple rule is to maintain a safety stock level that’s 50% of your lead time demand, that is, maintaining half the stock you use on average during reorder lead times. You can calculate this by multiplying your average weekly sales by your lead time in weeks and then dividing it by two.
However, this basic formula doesn’t consider your demand or lead time fluctuations. (We’ll discuss different safety stock formulas in the next section that consider these fluctuations, so you can choose the one that suits your situation.)
But it’s important to remember that while having an optimal safety stock level is important, carrying too much can be risky. The primary risk is increased inventory carry costs, a crucial consideration with the rising demand for logistics spaces, especially in urban markets with high eCommerce penetration.
Ultimately, the amount of safety stock you carry will depend on your risk tolerance as a business. A higher tolerance for the risk of running out of inventory means you can carry inventory levels that require the least amount of capital expenditure.
High-risk inventory planning leads to higher profits and frees up capital to invest in other areas of the business.
Conversely, a lower risk tolerance means your top priority will be insuring against stockouts. A low-risk approach requires greater capital expenditures but usually leads to greater customer satisfaction.
A standard safety stock formula is a good starting point for calculating the safety stock you need.
Safety Stock Formulas
Here are some popular safety stock calculations used by merchants worldwide.
Different formulas exist because every business has unique needs. The right formula depends on factors like demand variability, lead time, and profit margins. Choosing the appropriate formula helps you manage inventory efficiently and avoid unnecessary costs.
Basic Safety Stock Formula
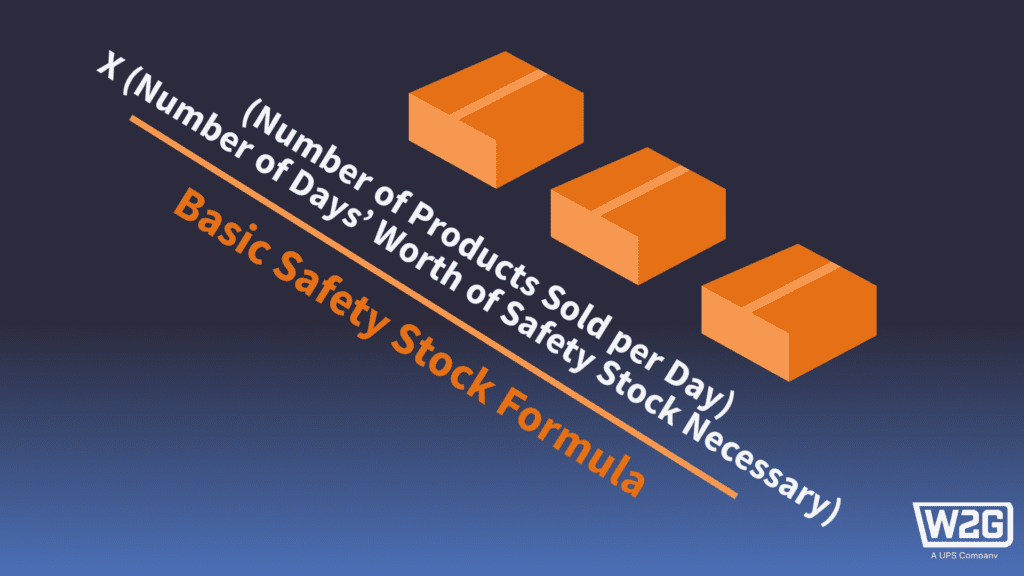
The basic safety stock formula is a simple method for calculating the necessary safety stock to maintain in your inventory. Use this formula when you have a consistent demand for your products and reliable lead times from your suppliers.
But why do you need safety stock if everything’s certain? That’s why this is a simple calculation you can use to keep safety stock as a preventative measure and it’s not ideal during fluctuations.
To calculate your safety stock using this formula, you need to multiply the average number of products sold per day by the number of days’ worth of safety stock you deem necessary based on your experience and risk assessment.
Safety Stock = (Average Number Of Products Sold per Day) ร (Number Of Days’ Worth of Safety Stock Required)
For instance, let’s say you sell an average of 50 units of a specific product per day, and your average lead time from your supplier is 7 days.
Based on your historical data and risk analysis, you determine that maintaining 10 days’ worth of safety stock is sufficient to mitigate potential supply and demand fluctuations.
Safety Stock = 50 units per day ร 10 days = 500 units
Max โ Average Safety Stock Formula
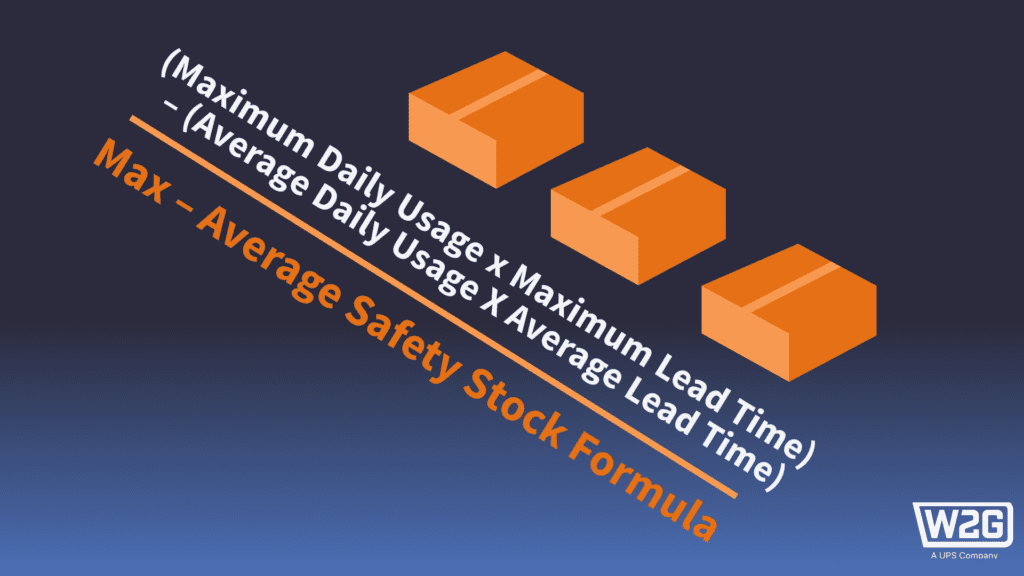
This formula is helpful to calculate the average safety stock you need to hold if there’s a risk of stockouts.
Businesses choose the Max โ Average Safety Stock Formula to account for demand and lead time variability, especially for critical items. This formula provides a more conservative approach by considering the maximum daily usage and maximum lead time, helping to minimize the risk of stockouts during peak demand periods or when facing potential supplier delays.
Itโs also straightforward and requires only four variables, making it easier for businesses to calculate and implement compared to more complex safety stock formulas.
You’ll need four key variables to calculate this safety stock formula.
- Maximum Daily Usage: It’s the maximum number of units you’ve sold in a day during a specified period. You may be accustomed to talking about your Average Order Volume (or AOV), but maximum daily usage is an outlier. Do an audit of your sales history over a fixed period of time and find the largest quantity sold in a single day.
- Average Daily Usage: It’s the average number of units you typically sell through in a day. This number is similar to AOV, which is often used by warehouses to estimate labor needs and plan warehouse layout, slotting, and pick paths.
- Maximum Lead Time: This is the maximum time it could take to receive a replenishment order from a supplier. To ensure enough safety stock, consider the worst-case scenario when finding your maximum lead time.
- Average Lead Time: This is the average number of days it takes to receive a replenishment order from your supplier.
With all of the variables in place, the formula for safety stock is:
Safety Stock = (Maximum Daily Usage X Maximum Lead Time) โ (Average Daily Usage X Average Lead Time)
For example, Kyra Electronics is an online retailer specializing in selling smartphones and accessories. They want to determine the appropriate level of safety stock to maintain for their flagship smartphone model to avoid stockouts and ensure customer satisfaction.
Given:
Maximum Daily Usage: 200 units (based on historical sales data during peak seasons)
Average Daily Usage: 100 units (based on average sales throughout the year)
Maximum Lead Time: 10 days (considering potential delays from the supplier)
Average Lead Time: 7 days (usual time taken for receiving replenishment orders)
Using the Max โ Average Safety Stock Formula:
Safety Stock = (Maximum Daily Usage ร Maximum Lead Time) – (Average Daily Usage ร Average Lead Time)
Safety Stock = (200 units ร 10 days) – (100 units ร 7 days)
Safety Stock = 2,000 units – 700 units
Safety Stock = 1,300 units
Heizer Render Formula
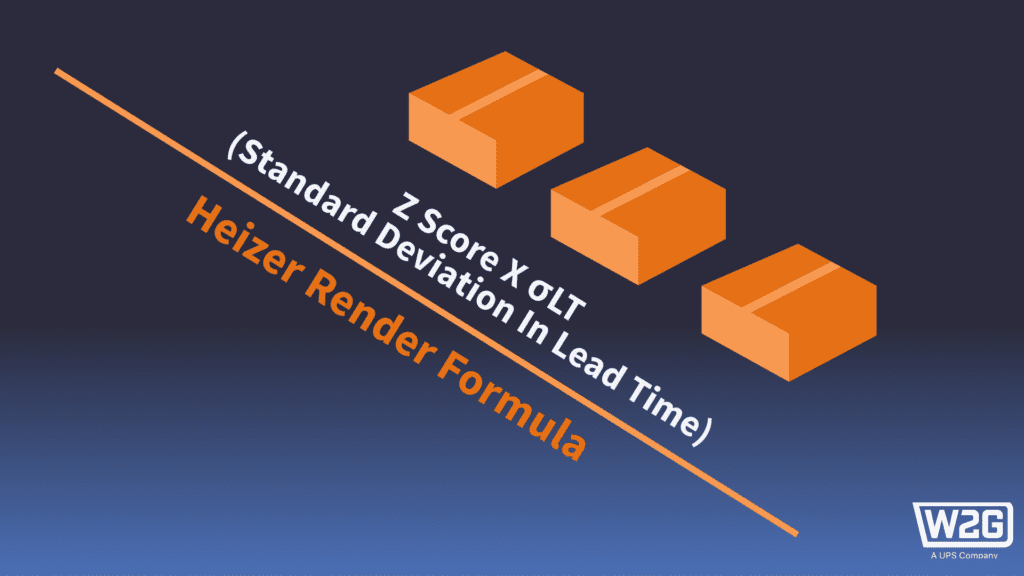
This formula helps you maintain a desired service level by ensuring you have enough stock to cover potential delays in lead time.
To calculate safety stock using the Heizer and Render formula, first, determine the appropriate Z score based on your desired service level and then, calculate the standard deviation in lead time (ฯLT).
Z score is a statistical measure that represents the number of standard deviations from the mean required to achieve a specific service level. In other words, it’s a way to understand how far a particular value is from what’s considered “normal” or “expected.”
Don’t worry about the calculations; you can find the Z score for your desired service level in the Z score table.
For example, a 90% service level has a Z score of 1.28, a 95% service level has a Z score of 1.64, and a 75% service level has a Z score of 0.67.
- ฯLT: The standard deviation in lead time (ฯLT) measures the variability in the supplier’s lead time, which is the time from when you place an order for materials to when the stock is received. To calculate ฯLT, you need historical data on lead times.
Once you have the Z score and ฯLT, you can calculate the safety stock using the formula:
Safety Stock = Z Score X ฯLT (Standard Deviation In Lead Time)
If you experience significant variations in demand, consider the following safety stock calculation.
Certainly! Let’s work through a real-life example using the Heizer Render Formula for safety stock calculation.
For example, Asteroid Company wants to maintain a 95% service level for their flagship product. The company has analyzed historical data on lead times and found that the standard deviation in lead time (ฯLT) is 2 days.
Given:
Desired service level: 95%
Standard deviation in lead time (ฯLT): 2 days
Step 1: Determine the Z score for the desired service level.
From the Z score table, a 95% service level corresponds to a Z score of 1.64.
Step 2: Calculate the safety stock using the Heizer Render Formula.
Safety Stock = Z Score ร ฯLT
Safety Stock = 1.64 ร 2 days
Safety Stock = 3.28 days
Interpretation:
To maintain a 95% service level, Asteroid Company should keep a safety stock that covers 3.28 days of lead time variability. Based on their average daily usage, this means that the company should have enough inventory on hand to cover an additional 3.28 days of demand.
For example, suppose Asteroid Company’s average daily usage is 100 units. In that case, they should maintain a safety stock of approximately 328 units (3.28 days ร 100 units per day) to ensure a 95% service level and account for potential lead time variations.
Greasley’s Formula
This is the most sophisticated safety stock formula among the ones we discussed and it’s useful for companies with both demand variabilities and lead time variabilities.
Safety Stock = Z Score X Standard Deviation in Lead Time (ฯLT) X Average Demand
Essentially, Greasley’s method adds the average demand component into the Heizer Render formula.
This is more realistic because your product’s demand might change seasonally or due to market conditions, for example, the surge in demand for Christmas ornaments before Christmas and the increased demand for hats due to a sudden temperature rise.
Example:
Sapphire Retail Store wants to maintain a 98% service level for their best-selling toy. The store has analyzed historical data and found that their supplier’s standard deviation in lead time (ฯLT) is 3 days. The average daily demand for the toy is 50 units.
Given:
Desired service level: 98%
Standard deviation in lead time (ฯLT): 3 days
Average daily demand: 50 units
Step 1: Determine the Z score for the desired service level.
From the Z score table, a 98% service level corresponds to a Z score of 2.05.
Step 2: Calculate the safety stock using Greasley’s Formula.
Safety Stock = Z Score ร Standard Deviation in Lead Time (ฯLT) ร Average Demand
Safety Stock = 2.05 ร 3 days ร 50 units
Safety Stock = 307.5 units
Interpretation:
To maintain a 98% service level, Sapphire Retail Store should keep a safety stock of approximately 308 units (rounded up from 307.5) of their best-selling toy. This safety stock level accounts for both the variability in lead time from the supplier and the average daily demand for the product.
Is It Possible To Have Too Much Safety Stock?
Carrying too much safety stock can lead to several risks such as:
- Decreased profitability for the business
- Inefficient use of resources like labor and equipment
- Reduced cash flow as capital is tied up in unsold inventory
- Increased carrying costs due to additional storage requirements
- Excess inventory-related cost since warehouse space is limited and storage rates are high
One tactic to increase safety stock without significantly increasing inventory carry costs is to carry fewer SKUs overall.
When looking at your sales history, youโll likely have a few top-performing SKUs that significantly drive your businessโs profitability. It may be wise to increase the quantities of those SKUs while eliminating your slow-moving SKUs entirely.
By carrying fewer SKUs, youโll significantly reduce your warehouse footprint, allowing you to carry greater quantities and keep more safety stock on hand.
When analyzing your SKU catalog and determining which SKUs you may want to discontinue, you need to find the right balance between specialization and having the variety of choices your customers expect.
Frequently Asked Questions (FAQ)
Now that we know how to calculate safety stock and why we need it, you might still have a few lingering questions, so letโs address them here.
How Do You Calculate Safety Stock?
There are many ways to calculate safety stock, but the most popular safety stock calculation is the Max โ Average safety stock calculation, which is shown below.
Safety Stock = (Maximum Daily Usage x Maximum Lead Time) โ (Average Daily Usage X Average Lead Time)
What Is the 50% Rule of Safety Stock?
The 50% rule of safety stock suggests maintaining a safety stock level equal to 50% of your average lead time demand (half of the stock you typically use during reorder lead times).
This is calculated by multiplying your average weekly sales by your lead time in weeks and taking half of that value. This rule provides a quick estimate without complex calculations but doesn’t account for demand or lead time fluctuations.
Why Calculate Safety Stock?
It’s important to have enough stock so that a sudden disruption in your material supply doesn’t stop your production and leave your customers unfulfilled, leading to lost sales.
Safety stock helps businesses avoid stockouts by preparing for unexpected spikes in demand and supplier delays. It ensures customer satisfaction, maintains strong relationships with suppliers and retailers, and helps avoid additional costs due to price fluctuations and rushed shipping.
Can Safety Stock Be Zero?
Safety stock can sometimes be zero, particularly for items with highly predictable demand, short lead times, reliable suppliers, and if you don’t have storage space. This approach is more common in just-in-time (JIT) inventory management systems, where businesses closely coordinate with suppliers to receive goods exactly when needed, minimizing the need for safety stock.
However, setting safety stock to zero is generally not recommended for most businesses, as it leaves no buffer against unexpected demand spikes, supply chain disruptions, or other uncertainties, which can lead to stockouts and lost sales.
Even in JIT systems, a small amount of safety stock is often maintained for critical items to minimize risks.
Whatโs the Difference between Safety Stock and Buffer Stock or Minimum Stock?
Safety stock is the extra inventory you need to avoid the risk of running out of stock due to changes in buyer demand or supplier lead times. It ensures a company can meet customer demand, even with unexpected fluctuations.
Buffer or minimum stock are broader terms that include safety stock and additional inventory held for other reasons.
Simply put, safety stock has excess inventory on hand for any unexpected circumstance, whereas buffer stock primarily has excess inventory to cater to spikes in sales.
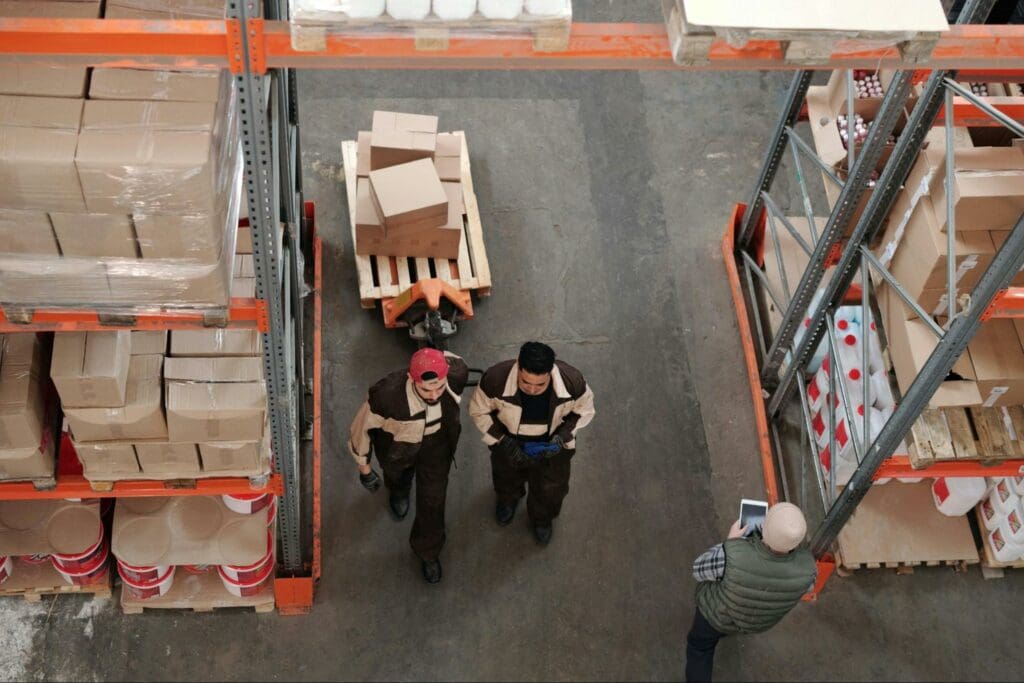
Going Forward: Automate Safety Stock Formula for Efficiency and Accuracy
Now that you know the important safety stock formulas and best practices, you’re well-equipped to avoid the costly consequences of stockouts and keep your customers satisfied.
However, as your brand grows, manual safety stock calculation can become increasingly time-consuming and complex. To ensure accuracy and efficiency, consider partnering with a tech-enabled 4PL like Ware2Go.
With access to automated inventory reporting tools and expert guidance on SKU optimization, reorder points, and inventory distribution, you can leave your inventory management worries behind and focus on growing your business.
If you’re looking for a fulfillment partner with an intelligent inventory management solution, talk to one of our fulfillment specialists today.