Want to enhance inventory management? Our ending inventory formula guide helps you reduce costs and efficiently optimize stock levels. Learn more now!
The ending inventory formula is essential for businesses, yet many struggle to use it effectively. As you close out your financial year, you might realize your inventory numbers donโt add up. Panic sets in as you try to reconcile the differences, knowing that inaccurate inventory could lead to tax issues, misreported profits, and poor decision-making.
Download Ware2Goโs eBook to streamline your warehousing and fulfillment processes with effective inventory management techniques.
Imagine mastering the ending inventory formula and turning this potential nightmare into a strategic advantage. By confidently calculating your ending inventory, you can ensure accurate financial reports, make informed decisions, and stay ahead of the competition.
This article will help you understand the formulaโs importance, explore methods, and learn to apply them effectively to improve your businessโs financial health.
What Is Ending Inventory?
Ending inventory is an inventory accounting term that represents the total value of inventory you have ready to sell (or finished goods). Most businesses calculate ending inventory at the end of an accounting period, including it as an asset on their balance sheet for calculating taxes and accurately estimating the value of their business.
Although the most accurate methods of calculating ending inventory include a physical inventory count, the purpose of calculating it is to determine the value of the inventory on hand, not the number of units. This is especially important when determining the value of your business for obtaining financingย or pitching to potential investors. There are a number of methods that can be used to calculate ending inventory, and each method will yield a different value, even if the amount of inventory stays the same.
Why is Ending Inventory Important?
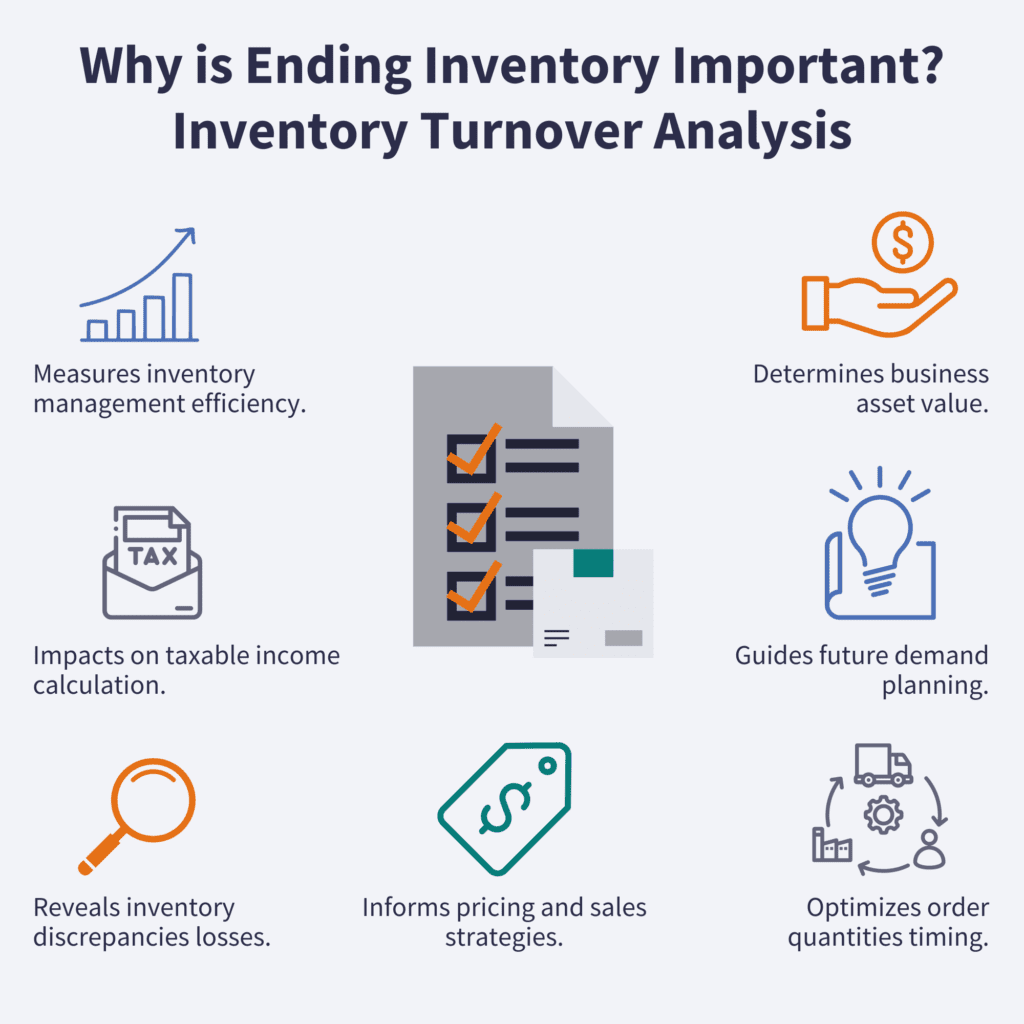
Calculating ending inventory not only helps with determining the value of your business but also cuts down on inventory shrinkage and helps with forecasting. Building a forecast based on the value of inventory rather than simply SKU velocity and total sales enables forecasting that keeps profitability in mind so you don’t run the risk of selling yourself out of business.
It also helps with proactive supply chain planning by connecting inventory forecasting and availability to a promotional schedule. This way you can align your marketing efforts with SKU availability to strike the right balance of keeping inventory carry costs low without missing out on potential sales.
Calculating ending inventory can particularly add value for fast-growing brands and enable them to mature their business operations in the following key ways.
Inventory Turnover Analysis
Ending inventory is integral to calculating the inventory turnover ratio, a key metric for assessing how efficiently a company manages its stock. It helps identify slow-moving SKUs that could be damaging margins with increased inventory carry costs. Find inventory turnover by dividing the cost of goods sold (COGS) by the average inventory (which includes beginning and ending inventory). A high turnover ratio may indicate effective inventory management and strong sales, while a low ratio might signal overstocking or sluggish sales.
Valuation of Business
Ending inventory directly impacts a businessโs balance sheet and overall valuation. Higher inventory values contribute to greater current assets, reflecting a stronger financial position. Accurately accounting for ending inventory ensures potential investors or buyers have a clear view of the businessโs operational efficiency and profitability.
Tax Reporting
Ending inventory plays a critical role in determining taxable income by affecting COGS. Different valuation methods, such as FIFO (First-In, First-Out) or LIFO (Last-In, First-Out), can significantly alter reported income. A precise ending inventory valuation ensures compliance with tax regulations and optimizes the tax burden. And choosing the right valuation method optimizes costs in terms of taxes and fees.
Budgeting & Reporting
Ending inventory figures are foundational for accurate budgeting and forecasting. They inform purchasing and production plans by identifying high-demand SKUs that should be prioritized for replenishment. Moreover, understanding ending inventory supports better cash flow management by aligning inventory costs with sales trends.
Identifying Shrinkage & Loss
Comparing calculated ending inventory with physical inventory counts can uncover shrinkage caused by theft, damage, or administrative errors. Recognizing these discrepancies early helps businesses create more effective prevention strategies, improve operational accuracy, and protect margins.
Supply Chain Management
Ending inventory data is vital for making informed supply chain decisions. It enables businesses to optimize order quantities and timing, to balance the risk of missed sales opportunities against the risk of overstocking. The result is reduced inventory carry costs and improve overall supply chain efficiency.
Pricing & Sales Strategies
Ending inventory insights help businesses refine pricing and sales strategies by identifying slow-moving or obsolete stock. This data can inform strategy around markdowns, promotions, or liquidation plans to minimize losses. Additionally, understanding inventory turnover aids in seasonal inventory planning, ensuring businesses capitalize on peak demand periods without overburdening cash flow.
Ending Inventory Methods and Examples
At the most basic level, ending inventory is:
- Ending inventory = beginning inventory + purchases – COGS
beginning inventory + net purchases โ cost of goods sold (COGS)
Much like calculating WIP inventory, the first variable, beginning inventory, is found by carrying over the ending inventory from the previous accounting period. There are a few methods for calculating ending inventory that will result in different values. The physical number of units on hand will not change, but their estimated value will change based on the method used.
How to Find Ending Inventory Using FIFO
FIFO (First in First Out) is an inventory tracking protocol that assumes that the first units of inventory purchased or manufactured are the first to be sold. Using FIFO to calculate ending inventory means that the cost of purchasing the oldest inventory (or First in) will be allocated first to COGS, and the cost of the newest inventory will be allocated to ending inventory. This means that if the cost of purchasing or manufacturing your inventory increased since your oldest inventory was purchased, your COGS will be lower for the first items sold (First out).
For example, you begin an accounting period with 100 units of a certain SKU purchased (or manufactured) at $5 per unit. Then later in the accounting period you place a replenishment order for 100 more units at $7 per unit. The entire accounting period, you sell 125 units. To calculate your COGS, you’ll use the cost of the first 100 units you ordered (5 x 100 = $500) plus the 25 units sold from your replenishment order (7 x 25 = $175), so your total COGS for that accounting period will be $675.
FIFO (First-In, First-Out) Method:
Ending Inventory = Beginning Inventory + Net Purchases – COGS (Where COGS is calculated using the oldest inventory first)
Using the ending inventory formula with this COGS value would give you the following ending inventory:
$500 (beginning inventory) + $700 (net purchases) โ $675 (COGS) = $525 (ending inventory)
How to Find Ending Inventory Using LIFO
LIFO (Last in First Out) is an inventory tracking protocol that assumes that the inventory purchased or manufactured most recently were sold first. Using LIFO to calculate ending inventory means that older inventory is allocated to ending inventory, while newer inventory (Last in) is allocated first to COGS. This means that if the cost of purchasing or manufacturing your inventory increased since your oldest inventory was purchased, your COGS will be higher for the first items sold (First out).
Let’s assume again that you have 100 units of a single SKU purchased (or manufactured) at $5 per unit. Then later in the accounting period you place a replenishment order for 100 more units at $7 per unit. Then, throughout the entire accounting period, you sell 125 units. To calculate your COGS using the LIFO method, you would use the cost of last 100 units you ordered (7 x 100 = $700) plus the 25 units you sold from your original order (5 x 25 = $125), so your total COGS for the accounting period would be $825.
LIFO (Last-In, First-Out) Method:
Ending Inventory = Beginning Inventory + Net Purchases – COGS (Where COGS is calculated using the newest inventory first)]
Using the ending inventory formula with this COGS value would give you the following ending inventory:
$500 (beginning inventory) + $700 (net purchases) โ $875 (COGS) = $325 (ending inventory)
How to Find Ending Inventory Using WAC
WAC (weighted average cost) averages your COGS based on the cost of all inventory purchased during the accounting period divided by the total number of units on-hand. Using the WAC method to calculate ending inventory means that all units are given the same (weighted) value.
Formula for calculating WAC:
Weighted Average Cost (WAC) Method: WAC per unit = Total Cost of Inventory / Total Number of Units COGS = WAC per unit ร Number of units sold Ending Inventory = Beginning Inventory + Net Purchases – COGS
We’ll assume again that you have 100 units of a SKU purchased (or manufactured) at $5 per unit. You then place a replenishment order for 100 units at $7 per unit. Throughout the accounting period you sell a total of 125 units. Using the WAC method, you would add the total cost of both orders (500 + 700 = $1,200), then divide that by the total number of units (1200 / 200 = $6 per SKU) Your COGS would be calculated by multiplying your weighted average cost of $6 by the number of units you sold (6 x 125) for a total of $750.
Using the ending inventory formula with this COGS value would give you the following ending inventory:
$500 (beginning inventory) + $700 (net purchases) โ $750 (COGS) = $450 (ending inventory)
Alternate Ending Inventory Formulas
In the three examples above, the same formula is used to calculate ending inventory, but the method of determining the cost of goods sold (COGS) variable was different, which led to a different ending inventory valuation, although the physical number of units on hand never changed. There are 2 other common ways to calculate ending inventory that are slightly more complex and use a different formula altogether: the gross profit method and the retail method.
How to Find Ending Inventory Using the Gross Profit Method
The gross profit method is useful for a quick estimation of ending inventory, but is not appropriate for end-of-year accounting because it doesn’t include a physical count of inventory. The formula includes a new variable, the cost of goods available for sale, which is calculated by adding the cost of beginning inventory with the cost of replenishment inventory.
The gross profit ending inventory formula is:
Cost of goods available for sale โ COGS = ending inventory
For the sake of simplicity, we’ll use the same company example as our previous formula. In this example your company had a beginning inventory of 100 units purchased at $5 each, then placed a replenishment order of 100 units at $7 each. This gives a total cost of goods available for sale of $1,200.
The next variable is a familiar one: cost of goods sold (COGS), but we’ll use gross profit margin to determine its value. Using our same example, we’ll assume that the SKU’s in question are sold for $10, yielding a gross profit margin of 40%. Again, we’ll assume you sold 125 units throughout the accounting period for a total of $1,250 in sales. You would then multiply your total sales by your gross profit margin ($1,250 x 40%) for $500 in COGS.
To find ending inventory, simply subtract your COGS from your cost of goods available for sale. ($1,200 โ $500 = $700 ending inventory)
How to Find Ending Inventory Using Retail
The retail method is similar to the gross profit method in that it doesn’t require a physical count of inventory. If you have the variables available it can be a quick way to get an estimate of ending inventory, but it is not a very reliable method, especially if your prices change regularly. For most ecommerce and multichannel sellers, prices may change daily using tools like automatic repricers to help win the buy box and stay at the top of search algorithms. For those reasons, we won’t go into great depth about the retail method.
The basic formula for the retail method is:
Cost of goods available for sale โ cost of sales = ending inventory.
You can determine the cost of goods available for sale using the same method as the gross margin method. To find the cost of sales, you must multiply your total sales by your cost to retail percentage.
Best Practices for Accurate Ending Inventory
Implementing the following best practices regarding ending inventory calculations ensures precision, reduces discrepancies, and supports business decision-making.
Regular Audits & Reconciliations
Conducting regular audits to reconcile inventory records with actual stock (often called inventory cycle counts) is key to identifying discrepancies that can lead to over-selling.
Documentation & Record-Keeping
Maintaining accurate records of incoming shipments, sales, returns, and adjustments is key to to ensuring precise ending inventory calculations. It also simplifies audits and improves compliance with accounting standards.
Staff Training & Accountability
Well-trained staff are more likely to follow standardized processes, reducing errors. Establishing clear accountability also encourages adherence to best practices and fosters a culture of precision.
Data Analytics for Inventory Insights
Data analytics tools can optimize stock levels, predict future needs, and identify patterns such as slow-moving items or seasonal demand spikes. These tools can more easily identify trends to inform inventory management strategies.
Inventory Management Software
Advanced inventory management software automates tracking, streamlines data entry, and minimizes human error. Features such as real-time updates, barcode scanning, and integrated reporting ensure accurate and up-to-date inventory records, enabling precise ending inventory calculations.
Consistent Inventory Valuation Methods
Choosing and consistently applying an inventory valuation methodโwhether FIFO (First-In, First-Out), LIFO (Last-In, First-Out), or WAC (Weighted Average Cost)โis essential for accurate financial reporting. Consistency ensures comparability over time and aligns with accounting and tax regulations.
How Third Party Logistics Help Manage and Improve the Ending Inventory
Partnering with a tech-enabled 3PL can automate the process of monitoring inventory and make real-time inventory reporting available through an intuitive cloud-based WMS. A fulfillment partner should also have SLA’s that include regular inventory cycle counts with a 99% accuracy rate to ensure the best and most accurate data for calculating ending inventory.
Inventory Costs FAQs
Understanding the ending inventory formula is essential for accurate financial reporting and inventory management. Here are answers to some common questions about ending inventory.
What Is Ending Inventory on a Balance Sheet?
Ending inventory represents the value of unsold goods at the end of an accounting period and is listed as a current asset on the balance sheet. This value reflects the remaining stock that can be sold in future periods and directly impacts the companyโs financial position.
Does Ending Inventory and Beginning Inventory Mean the Same Thing?
While closely related, ending inventory and beginning inventory are not the same. Ending inventory refers to the stock remaining at the close of one accounting period, whereas beginning inventory is the same stock value carried over to the start of the next period. These values are sequentially linked, with ending inventory becoming the beginning inventory for the following cycle.
Does Ending Inventory Mean Closing Stock?
Yes, ending inventory is often synonymous with closing stock. Both terms describe the value of unsold goods at the end of a financial period. This figure is a key component in calculating the cost of goods sold (COGS) and assessing inventory management efficiency.
Simplify your ending inventory process with Ware2Go inventory management system
Don’t let inventory challenges hold your business back. Accurate tracking of beginning and ending inventory is no longer a luxuryโit’s necessary for growth and success.
Mastering your ending inventory process unlocks vital insights, drives smarter decisions, and optimizes cash flow. Today’s ending inventory becomes tomorrow’s beginning inventoryโthe foundation of your next successful year.
Ware2Go’s inventory management system streamlines operations with real-time tracking, automated calculations, and powerful analytics. Our tools transform inventory management into a strategic advantage.
Ready to elevate your inventory management? Don’t wait for the next financial year. Set your business on the path to greater efficiency and profitability now.